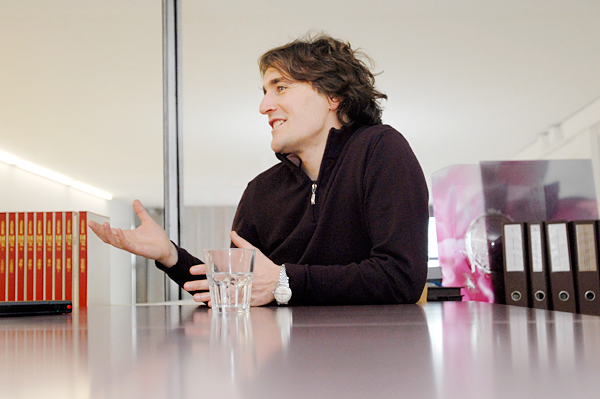
Langenthal, November 2010: For this year's Designers' Saturday Jörg Boner has installed himself in the old mill. Given carte blanche, the Zurich designer and his team erected a miniature factory of cardboard to present the current designs. The saw-tooth roofs of the walk-through model factory extend up to the ceiling of the low room. Inside a small, reduced area opens up - clad all around with cardboard. Straight from production and standing as if on a runway on a centrally placed table are two chairs: The new "Wogg 50" in bright orange and dark-gray glaze. After spending three years conceiving and developing it the plywood chair is to be presented next January at the imm Cologne as a mass-produced item. Sandra Hofmeister spoke to Jörg Boner about the development and design of the new item. Sandra Hofmeister: At the center of your miniature factory in Langenthal stands the "Wogg 50". Is the plywood chair a "factory item"? Jörg Boner: I don't think so. But I am in principle interested in "factory" conditions. The production means, opportunities and methods are extremely important in design. I don't believe in designs that evolve outside of this context, and are produced somewhere by someone. I prefer to visit firms, study their production processes and manufacturing methods and try to develop my designs from out of this context. This is more what is behind our homage to the factory. You are a carpenter by trade and your new chair is a wooden chair. Was the artisan background important for your design? Or were the methods of machine-based serial production the important factor? Jörg Boner: Naturally, as I was once a carpenter I thought I can work with wood and plywood better . Early on in the design process I got in touch with Becker - a German firm specialized in shaped plywood parts and which produces the individual elements of the chair today. I quickly realized that I had absolutely no idea about molded plywood. Industrial wood working is very complex especially when details are involved At any rate my experience as a carpenter was not really of much use to me for this project. Unlike plastic wood also stands in the furniture industry for a close connection with craftsmanship. Is that a misconception? Jörg Boner: The myth about plastic says that the material is much more industrial than wood. But in many cases that is not so. Plastic offers designers a fair amount of liberty as regards styling that is much more complicated with molded plywood. The "Wogg 50" consists of two parts - the seat area and backrest. Then there are the legs. For the molded plywood we developed two tools. The beech veneer sections were stuck on top of each other like thin layers of paper and pressed into shape in the tools. The production process is done entirely by machines - with some manual work being involved in clamping the components in the tools. Then the individual sections are assembled at Wogg in Switzerland. To what extent was the choice of molded plywood as material a conscious decision? Jörg Boner: First of all, Wogg wanted to develop a wooden chair from the start. The second point that influenced the choice of material has to do with production conditions: The firm Becker is located in the middle of a beechwood forest. The trees are cut and processed there. I find it sensible and exciting to process the material directly on site. Wood is a renewable raw material that has a certain naturalness and can be worked intelligently using a small amount of adhesive. That's what attracted me. The chair is not to cost more than EUR 400 in stores. How do you deal with such requirements as a designer? Jörg Boner: Ultimately, you talk about the actual production price and the manufacturing budget for the chair. I know Wogg so well by now that we can talk openly about cost calculations. I find it exciting when design has to develop within a cost framework! At any rate I would not like to design something and then ask a fantastic price for it. That is not professional, as I see it. But there are a few design schools which work exactly like that and see the design as an artistic act separate from all else, and which results in expensive, limited editions Do you see yourself more as an industrial designer than an artist? Jörg Boner: Most definitely. I relish the challenge of combining technical components with the formal requirement of development something contemporary. But it made producing a wooden chair especially difficult: We wanted to take into account all the conditions of industrial production and simultaneously design a chair that looks like it was designed in 2010, which not only speaks the contemporary formal language but is also based on the current state of knowledge. How can you recognize contemporary quality and state of knowledge when you observe the result? Jörg Boner: First it is the sparing use of the material. But I also attach importance to formal decisions: It is about an aesthetic that corresponds with what interests us today. That might sound vague but what I mean is a kind of individuality that lends the subjects important to us today a characteristic shape. Like a sculpture that has something to do with the here and now. Moreover, the two joints on the sides of the seat, where everything comes together are only possible in this style using the latest pressing technology. They come out of the tool as they are and there is no additional adhesive work as there was before. At any rate your own handwriting but also that of Wogg are clearly recognizable. How did you arrive at the individual curves and the bends in the backrest and seat area? Jörg Boner: To begin with we always develop ideas and sketch them. But then for the "Wogg 50" we quickly changed to producing 3D-drawings because they give you a better impression of the chair. As soon this concept coincided with the original idea we built a 1:1 model of cardboard. We used the pattern from the computer drawing to print out individual surfaces and then used this to construct the chair as a model. It might seem old fashioned to revert from the computer-generated 3D drawing to manual procedures but a great deal happens when you are constructing the model: A composition evolves that has its own language and a specific character. The presence of the object is only revealed by the cardboard model. Naturally, the shaped is programmed and you can control all the lines and curves using the computer but the presence only comes about with the model. Starting with a cardboard model we then reworked the computer drawing. We then repeated this procedure until everything was right. In other words, it takes many steps for the lines and curves to be given their final form. Like being fitted at the tailor's - where material is removed in some places or added in others? Jörg Boner: Exactly. Especially with a chair - some curves are fine when looked at from a certain angle, but when you turn the whole thing slightly something is not quite right. Then we correct the lines and transfer the corrections to the computer drawing. The curved backrest is worked onto the seat area from the outside and attached to its underneath. Where did this construction concept come from? Apart from its own furniture collection Wogg is known as a small firm that likes to experiment and develops innovative materials and constructions. Was there an assumption for the briefing that the chair would be produced at Wogg? Was it disappointing to work for so long on an item and then to give the result a number as a name? This time the number 50 rather than 42? Jörg Boner: (Laughs....) Well it is somewhat impersonal and as such perhaps a pity but we get on so well with the manufacturer and discuss everything so it was not a problem for me to accept the name. Our cooperation is exactly how I see the work of a designer. It is a partnership with all the highs and lows, and which we constantly work at. Ultimately, I feel happier for the chair to be named a number rather than the designer only being a number for the manufacturer. Are there plans to develop a chair family from "Wogg 50" - with lounge chairs, bar stools and possibly other items? But that was often the case recently. The "Tivoli Chair" by Verner Panton is now a family of Lounge Chair, bar stool and chair. Jörg Boner: I know it is often done, but I have yet to see a good family. Maybe you can create affinities. But then it is a new design. For example, the "Wogg 50" goes well with the table "Wogg 43". As a small brother a chair can look different to its very big sister, but it still belongs to a big family. At the end of the design phase the colors often tend to get neglected. How was that with "Wogg 50"? Jörg Boner: I find the color extremely important. Once when Mark Werder from Wogg and I traveled back to Switzerland from Becker during the course of a longer discussion we got onto the topic of paints for model ships. I then went and bought all the Tamiya paints from a model building store - it is a Japanese firm that makes paints for military planes and battleships. We then used these paints to develop our own color range comprising eight colors. For example, there are shades such as "dark sea-gray" - the names are much more attractive than the simple name of the chair itself. I can't claim to have much experience of colors but I do consider them to be important, and as part of the design. Colors have much more force than we imagine. At Designers' Saturday we immediately got into conversation with visitors about the colors. Colors are also fashion trends. It's possible that some colors will no longer be considered hip next year. What made you choose the colors you did? www.joergboner.ch
Jörg Boner: We had planned from the start to add the backrest to the seat area from the outside - so it stands out like some hair braids do. In design terms, I find that really attractive in design terms but technically it was a problem. Given the options at Becker we hit upon the idea of attaching the backrest from underneath using four flush-mounted screws on the seat area. Not only is this sturdy it also lends a certain flexibility making the backrest slightly springy. In construction terms the whole thing comes close to the upholstered "Visitor Armless Chair" by Eero Saarinen - it has a similar backrest but looks totally different. If you use a different design approach for this construction the chair quickly looks really old.
Jörg Boner: Actually, that was ruled out from the start. We wanted a wooden chair - then I proposed molded plywood as material. And given this choice it was clear that the chair could not be produced at Wogg. It is impossible for a small firm to use this specialized technology.
Jörg Boner: I hope not, and I can't see it happening somehow. You cannot simply adapt formal relations; the "Ant Chair" by Arne Jacobsen is not part of a family either. I know of many examples of chairs where the original idea worked well, but the expansions to create an entire seating program only works as a poor imitation of the original design. There is a harmony about a good chair as regards size, dimensions and its use. I don't think you can simply keep spinning and transferring these principles.
Jörg Boner: There are also beautiful garments whose fabric has the color scheme of a certain era and which nonetheless retain their quality beyond their time. Naturally, it is possible that some of our shades will no longer be good in a few years but ultimately the color - unlike the design and construction of the chair - is easy to alter. Having said that the colors must go with the design and do it justice.
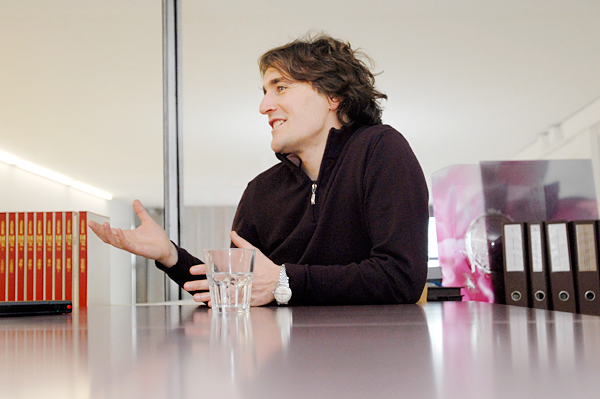
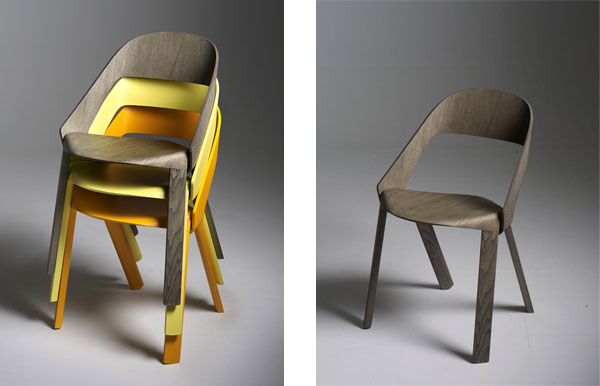
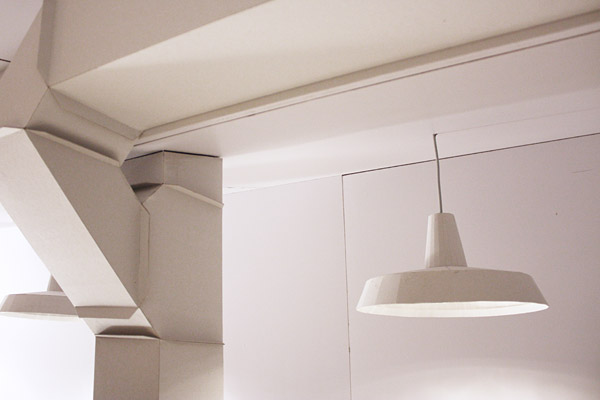
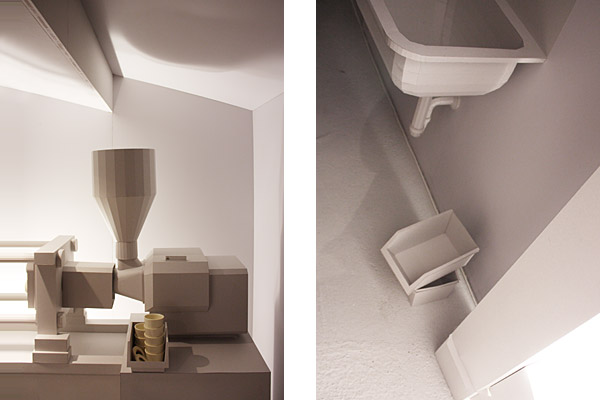
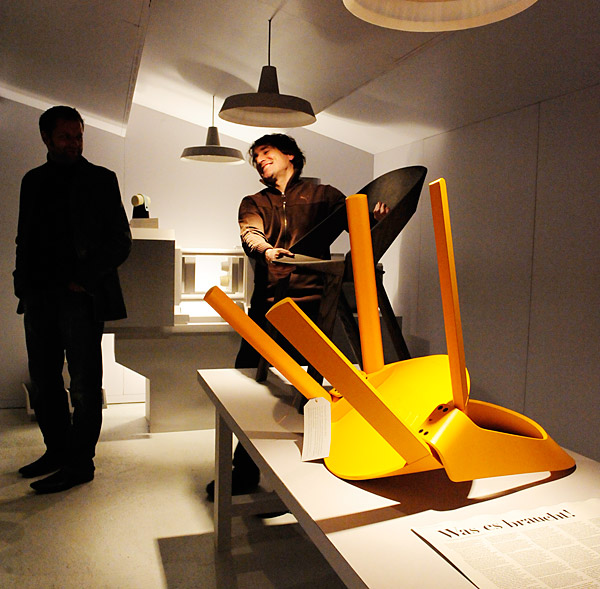
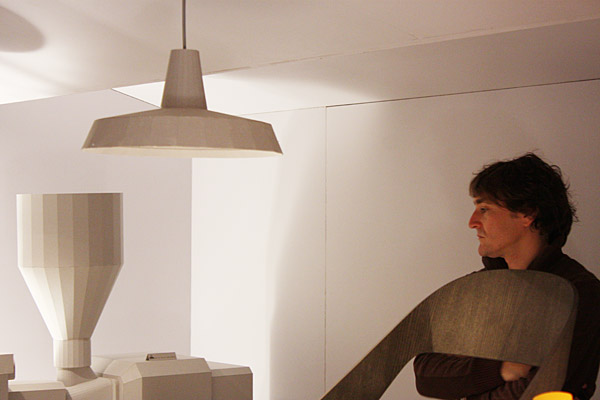
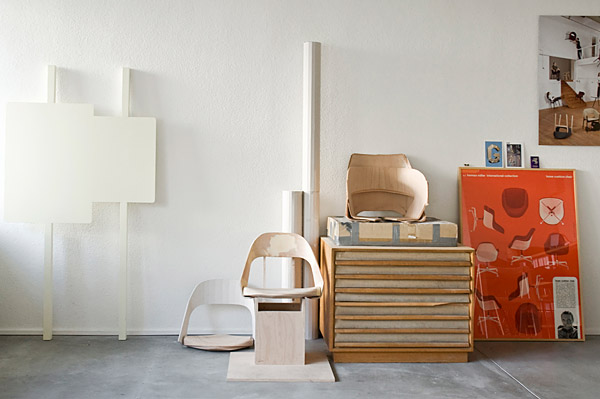
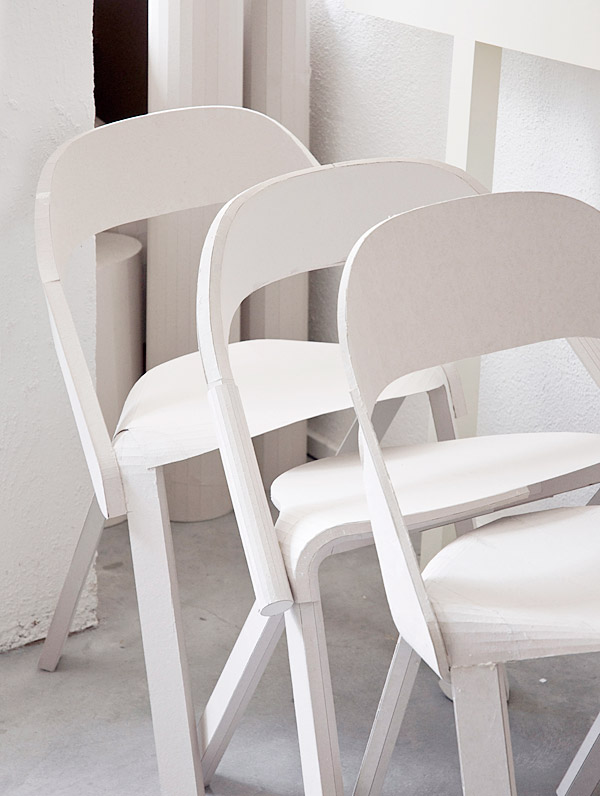