Not everything which has an ecological label these days is necessarily eco-friendly all the way through. Designer Tom Dixon, who has stressed the use and development of sustainable products right from the beginning of his career, recently brought out the "Ecoware" homeware range. These simple plates and cups are manufactured, it is claimed, from biologically degradable material, which is derived from bamboo fibre, one of the fastest growing natural raw materials. Rumour now has it that a polyamide - not exactly well-known for its compostability, is added to the organic material as a binder.
The creative atmosphere in which research into innovative eco materials is currently being conducted is reminiscent of the early stages in the development of plastic. This has left its mark on 20th century design like no other material, but has, at the same time, also damaged the environment. Just as, a good three quarters of a century ago, the combinations and applications for the then brand new plastics were still being tested out - to a certain extent in an alchemistic process of 'trial and error' - so now, at the beginning of the 21st century, there is no less of an enthusiastic and experimental mood as far as eco-materials are concerned.
The "green requirement" is today, unquestionably one of the most crucial parameters in the development of new materials. More and more research institutes, designers, and medium-sized companies are working flat out on materials which are either biologically degradable or can be recycled. More and more alternatives to traditional materials are being discovered and, with the materials, new fields of application, too. Many of the biologically degradable materials are new creations derived from substances which emerge as by-products in the processing of natural raw materials. And many recycled materials are themselves mostly recyclable again, without, however, the process being repeatable ad infinitum. One of the crucial issues in allocating green credentials to a given material is an ecologically efficient production process which involves a reduction both of waste and of long transport distances. The energy balance sheet within the company also plays a role, as does the relationship between what goes into the production and the quality and durability of the material that results. An 'eco' label only makes sense if there is unequivocal causal justification.
As far as recycled materials are concerned, one is struck, not only by the number and variety of the re-processed materials, but also by the growing number of possibilities for their use. Many of these new materials represent well-established functional alternatives to plastics or wood. Well is the name of a German company that uses a compression procedure without any binder to produce a flexible material called 'Wellboard' from old paper. Wellboard is used in furniture manufacture and as panelling for counters and walls in shops and exhibition stand construction. The Spanish company Lasentiu was founded in 2001 on the principle of recycling plastics from separated waste. The wood substitute 'Syntrewood' produced by Lasentiu using their recycling process is an adhesive-free, non-toxic material containing between 85 and 90 per cent polyolefine. Like wood it can be cut, drilled and even glued. It is water-resistant and significantly cheaper to buy than its natural antecedent. 'Syntrewood' is intended for use, principally, for constructing the inner parts of chairs.
Once they lose that typical look of recycled materials, the latter are increasingly establishing themselves in the world of design. Vitrohue are a company producing shiny red, green and blue decorative stones from tumbled, recycled glass; they can be used as garden decorations outside, or inside to create translucent mosaics. The Brazilian firm of Ekobe specialises in industrial waste from production processes, which is also an important area for recycling. The company uses what is left over from the processing of coconuts to create really fantastic natural tiles, which have been developed for use as wall panelling or floor covering. With their earthy colour and lively texture, reminiscent of dried figs, these avant-garde eco tiles which go best with icons of classic modernism like the 'Barcelona Chair' - and not only in publicity photos - are a good example of the engaging aesthetics that can attach to recycled materials. Most important among the boom markets for sustainable materials is the bioplastics market, where global production has been growing recently by 20% a year. What at first sounds like a contradiction, turns out, in this case, to be sustainable because these new bioplastics are either bio-degradable or bio-based. For the materials scientist there is nevertheless the problem that better bio-degradability must always be paid for in terms of poorer quality of the material. The art is finding the balance. Two bio-degradable and, in part, bio-based plastics have already been perfected by BASF and are now on offer as 'Ecovio' and 'Ecoflex', both of which received the "iF material award" in 2007. The elastic, water and tear resistant material 'Ecoflex' is based on petrochemicals and is particularly suitable for the production of packaging. 'Ecovico' consists on the one hand of 'Ecoflex' and on the other of a polylactic acid derived from maize. Its uses include laminates for packaging and breathable films in the hygiene sector.A no less ground-breaking bio substitute comes from the German company Tecnaro. Their thermoplastic material 'Arboform', also called 'liquid wood' was developed by the company's founders at the Fraunhofer Institute for Chemical Technology. 'Arboform' is completely biologically degradable, can be moulded like plastic and is intended chiefly for use in the production of injection moulded parts. This eco-material is manufactured on the one hand from organic lignin, a by-product of paper processing that comes from the walls of plant cells and, on the other, from natural fibres such as flax, hemp or sisal. It can be used in the manufacture of housings for loudspeakers and similar applications, but can also be used to produce the tiniest motor parts, since 'Arboform' is much stronger and more rigid than wood.
Many textiles, nowadays, are also biologically degradable. Climatex Lifecycle have developed a compostable upholstery fabric for Swiss-based Rohner Textil AG using natural 'ramie' bast fibre. The German firm of Barkcloth manufactures its so-called 'barkcloth' from the bark of the matuba fig tree. The extent to which the transport costs for the tree bark - which comes from Uganda - can be reconciled with the overall requirements for ecological acceptability in the case of 'Barktex' is, however, not immediately obvious from the consumer's point of view. The question of transport distances also arises in the case of bamboo, which currently represents the epitome of a natural raw material like no other, but which grows principally in far-off China.
Natural raw materials which initially appear, in themselves, to contain great ecological promise, must also demonstrate their green credentials in terms of sustainable cultivation and processing. Moso, the European market leader for bamboo products, demonstrates careful ecological providence in the way it processes these rapidly lignifying grasses, by deriving the energy necessary for the manufacturing process principally from burning bamboo shavings and other waste. It is also becoming more and more self-evident that we need a more environmentally conscious attitude when it comes to the planting, husbandry and processing of European wood. But requirements for sustainability of this kind cannot yet be applied entirely consistently. IKEA, international suppliers of furniture and furnishings, who committed themselves very early on to a comprehensively ecological company concept, have experienced bottlenecks this summer in the supply of ecologically acceptable woods from sustainable sources. "The certification of the forests took longer than expected, especially in China and Russia," IKEA explained. In order to avoid empty displays on the sales floor, some 'bad' woods found their way onto the shelves. Exceptions and uncertainties are all part and parcel of the process of innovation. But that we are, by now, well on the way, there can be no doubt.
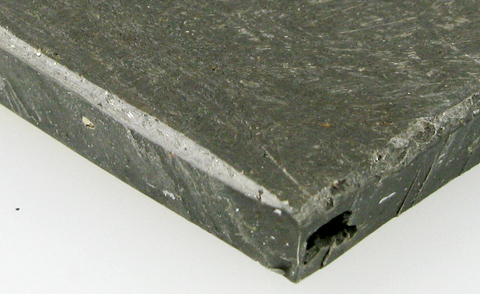
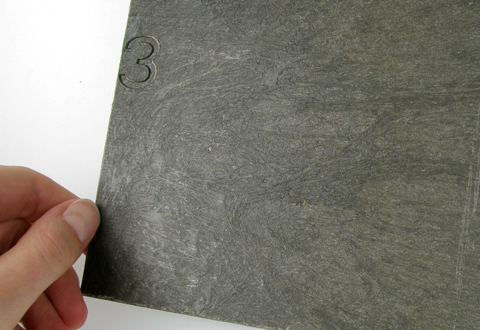

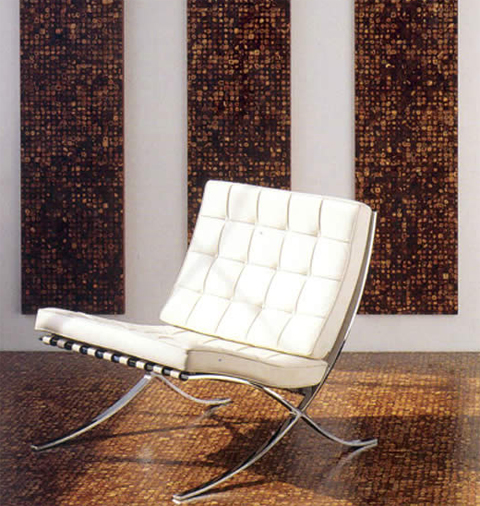
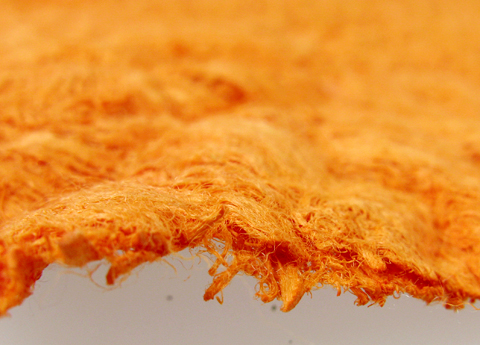
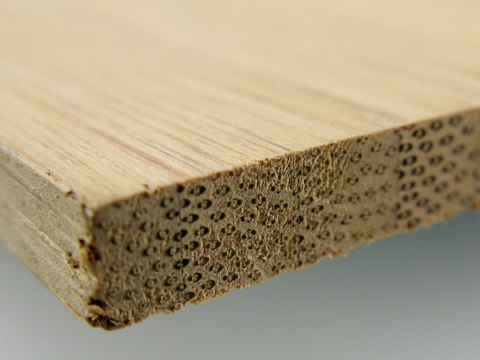
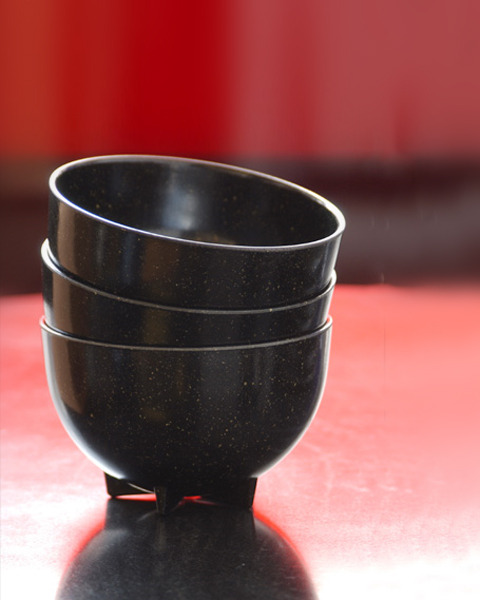
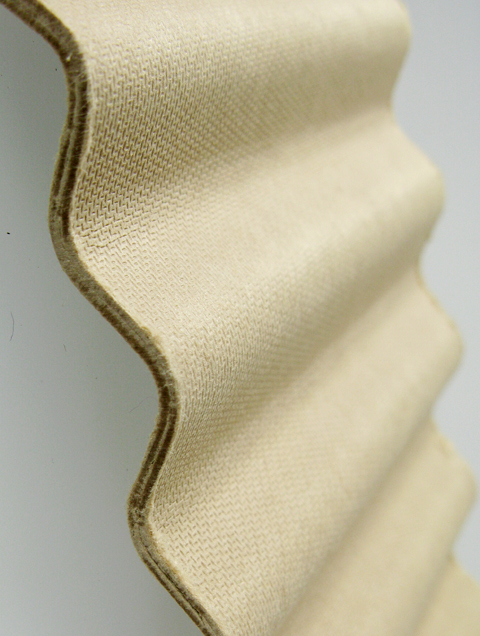
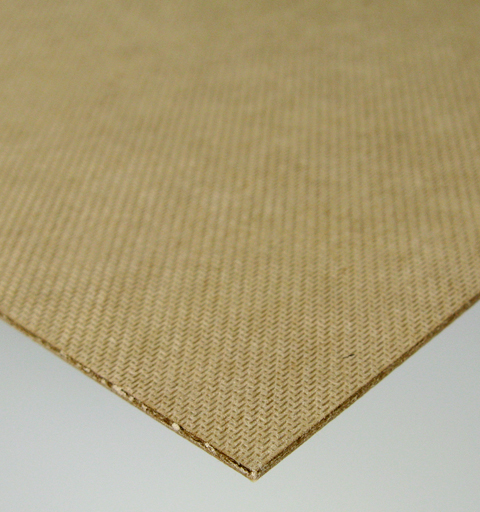
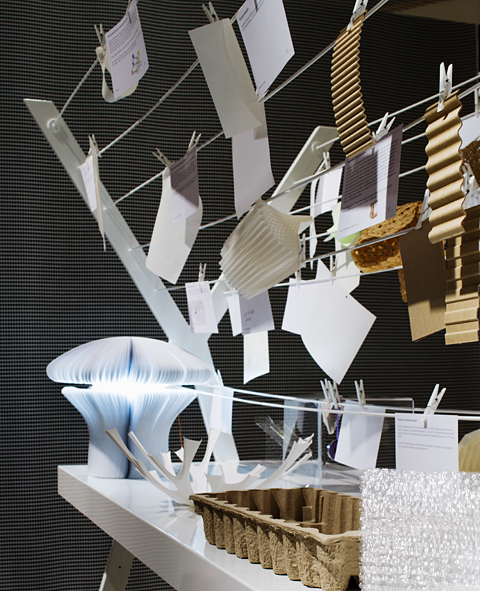
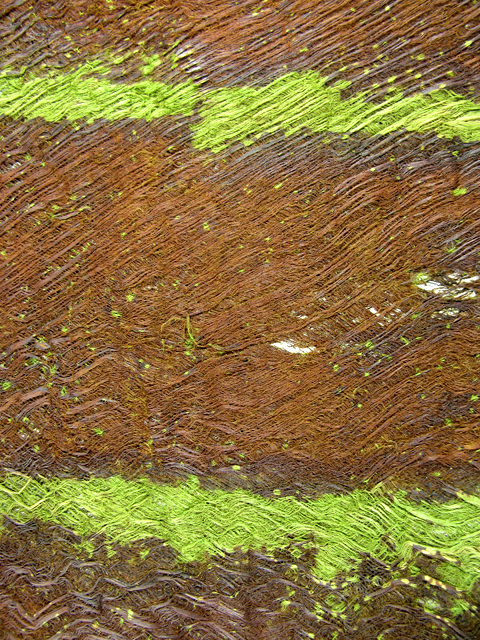
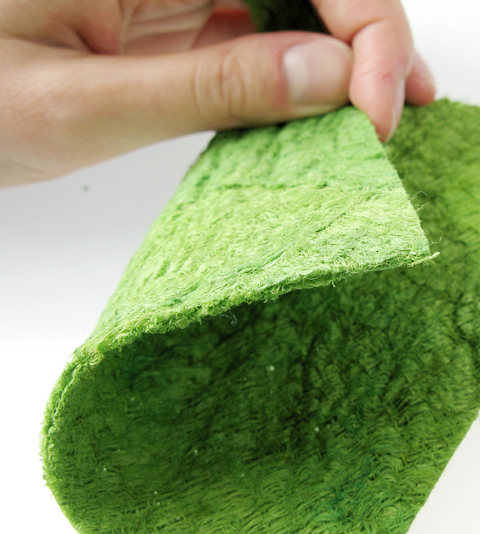
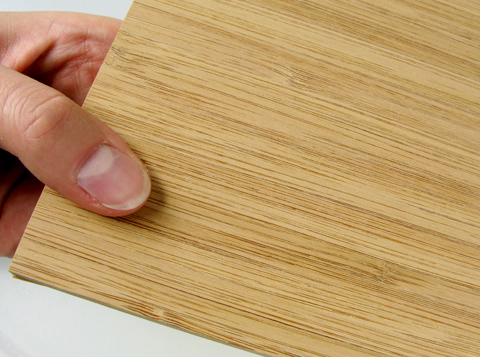