REVIEW – HEIMTEXTIL 2024
Digital and analogue
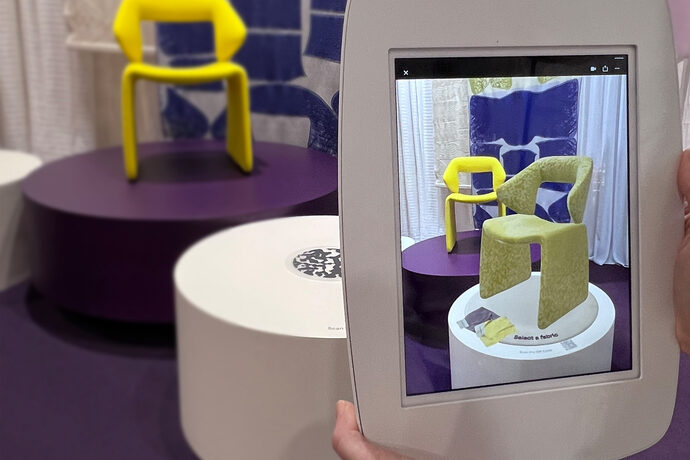
Augmented Weaving is an experimental research project on the technique of jacquard weaving and digital forms of craft, exploring physical, digital and virtual tools for the production of textiles and forms. For the installation at Heimtextil, Augmented Weaving have applied their experimental working methods to the "Suit" chair, designed by Monica Förster Design Studio for Artifort. The fabrics are designed directly on the 3D model of the chair and numerous designs and colour options can be tested digitally without wasting material. The example provides an insight into the possible workflows, which range from digital conception to the physical production of customised products on request.
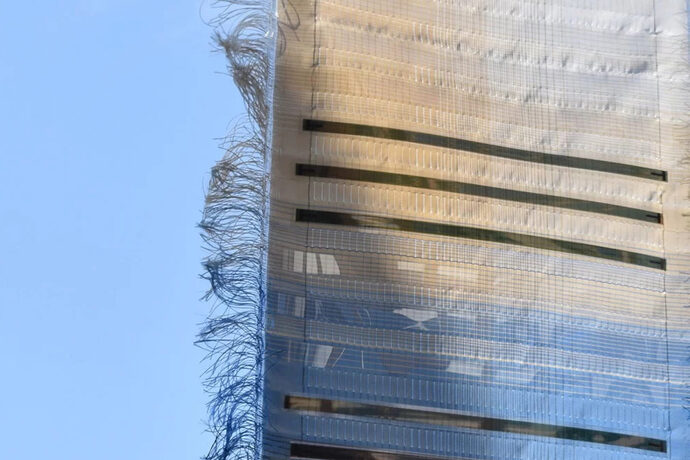
Studio Pauline van Dongen and Tentech have developed "Suntex", a solar textile that combines the flexibility, tactility and design freedom of textiles with the energy generation potential of solar technology. By weaving organic thin-film photovoltaic panels (OPV) into a textile, a smart and lightweight material is achieved. The structure of "Suntex" is modular and is intended to offer architects a particularly high degree of design freedom. According to Studio Pauline van Dongen, a speculative design study on the Westraven building in Utrecht shows that "Suntex" installed on three of the four façades could generate the energy for all the lighting needed in the spaces over the course of a year.
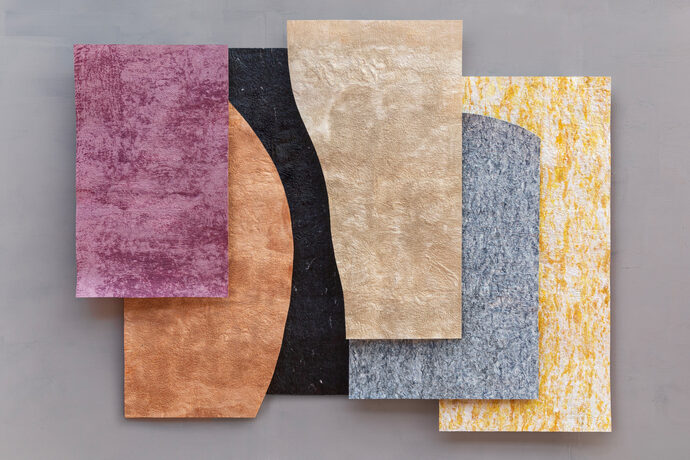
Studio Sarmite is a material design and research studio focussing on the transformation of industrial waste and its by-products into new circular concepts. In their work, designers Sarmīte Poļakova and Mara Berzina focus on the transformation of industrial waste and various by-products into new circular concepts. "(Un)woven" is a new bio-textile concept made from low-grade textile fibres that was developed as an alternative to the traditional textile recycling process. A unique production process transforms textile blends into a lightweight bio-textile suitable for fashion, interior and product design applications. The robust material can be recycled and used again and again for new production cycles. Together with Roua Atelier, Studio Sarmite has also developed a dyeing method for blended fabrics that is directly integrated into the production of the biotextile.
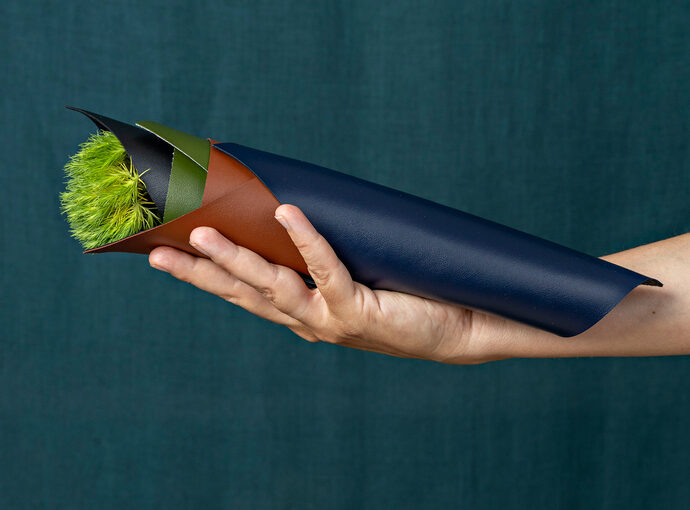
Leather alternatives: companies such as Von Holzhausen ("Banbu"), Desserto and Revoltech ("Lovr") are developing sustainable plant-based textiles that look and feel similar to leather. Bamboo, cactus or hemp provide the raw material for textile solutions that are biodegradable and have a minimal ecological footprint. Thanks to the possibility of individualising the result in terms of colour and texture and their robust properties, they can be used in a wide range of applications from interior design to vehicle upholstery.
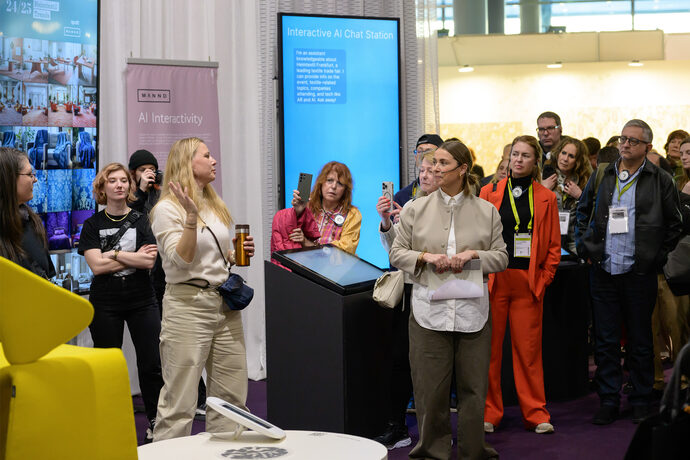
Mannd: The extent to which artificial intelligence can serve as a tool in the textile industry is demonstrated by an application example from Mannd at Heimtextil: the AI installation, conceived in cooperation with Spott trends and business, offers the opportunity to create your own designs by means of short questions from the AI – such as the desired material, its colour scheme or the place of use. An interactive AI chat station can also be used to answer questions about Heimtextil Frankfurt, textile topics and digital technologies such as AR, AI and ASMR.
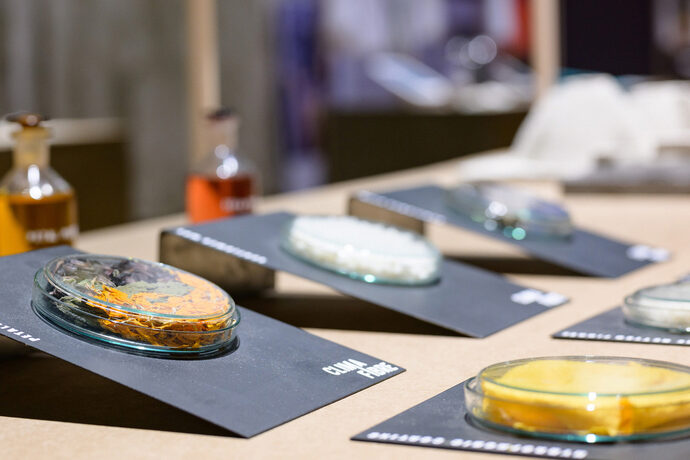
Radiant Matter is a design-oriented biomaterial start-up that has set itself the task of reducing the textile industry's dependence on plastics, metals and minerals extracted from crude oil as a colour material resource. The focus is on sustainable embellishment components and surface coatings. The first product is a BioSequin: biodegradable sequins made from renewable cellulose that produce brilliant shimmering colours that are non-toxic, colourfast and pigment-free. Their glittering metallic lustre is free from minerals, metals and associated mining, according to Radiant Matter.
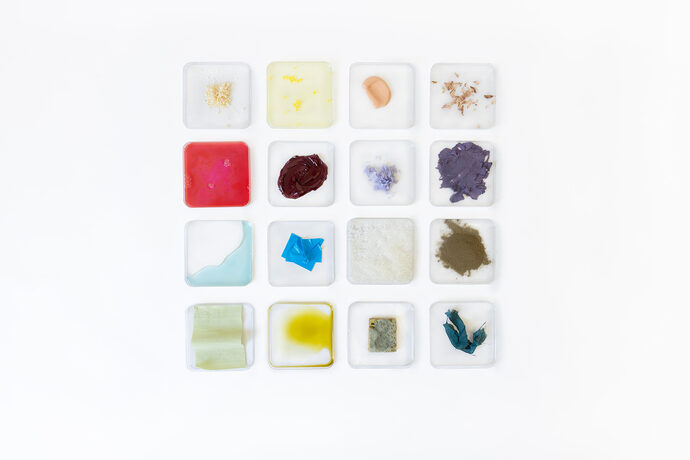
The bioresins and technical biocomposites by Pond Cycle are based on carbohydrates from plant material. They are more sustainable and durable than conventional plastics made from petroleum. The products can be used in existing industrial equipment and production facilities and are available both as a pure resin and as a premix with selected natural fibres, which reinforce the resin and give it individual technical properties.
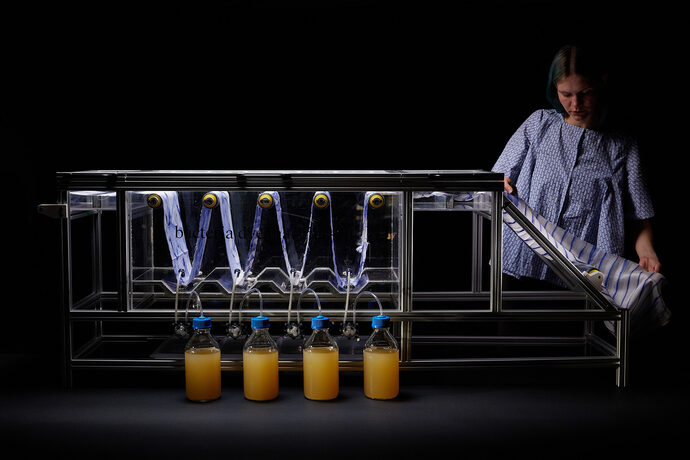
Charlotte Werth is a graduate of Central Saint Martins MA Material Futures, works at the intersection of textile and bio-design and has spent six years researching bacterial dyeing processes. During the design residency at Maison/0, she developed the project "Automating Violacein", a chemical-free nutrient bath that utilises the dyeing properties of a bacterium and then sterilises the fabric using an energy-saving UV lighting system. "As a designer, I want to learn from and with nature. My first step is to observe the natural world and gain new insights for my creative practice. This is how I discovered Janthinobacterium lividum, a wild, soil-dwelling bacterium that naturally produces colour. This biomimicry approach enables me to use new bio-based dyeing processes for textiles," she says.
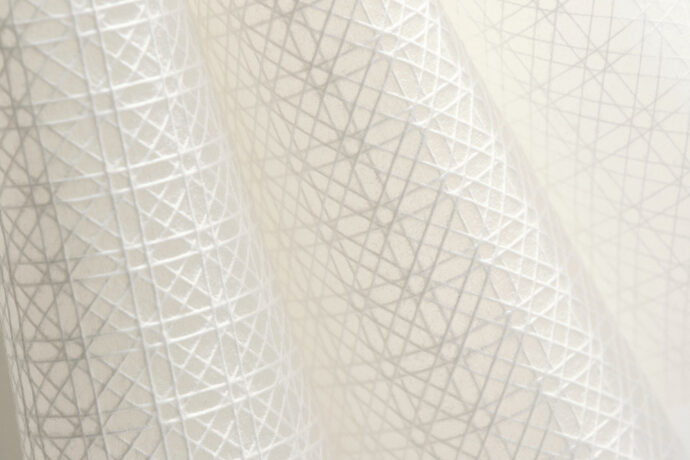
The biomaterials start-up Modern Synthesis is developing a microbial textile platform that enables the conversion of agricultural waste into nanocellulose. The fibres can then be mechanically formed into the desired shape and structure, avoiding material waste. The non-toxic and biodegradable textiles are thus customised in feel and appearance without using animal or artificial origins.
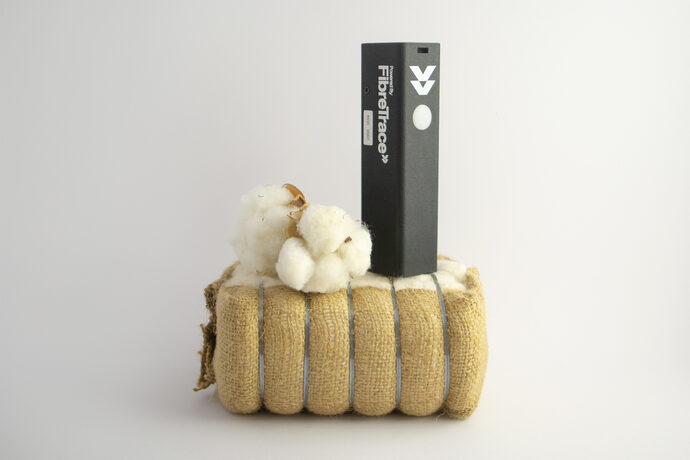
FibreTrace offers solutions for a transparent textile supply chain, such as the free digital tool "Mapped", which supports companies with transparency, supplier allocation and compliance with international import regulations. Information can be centralised and constantly accessed at every stage of production and logistics. FibreTrace wants to help ensure that every person in the textile supply chain has the opportunity to take direct responsibility for reducing the environmental impact of the global industry, including consumers. They can read the background information via a QR code on the product and thus choose an offer with a transparent and sustainable supply chain.
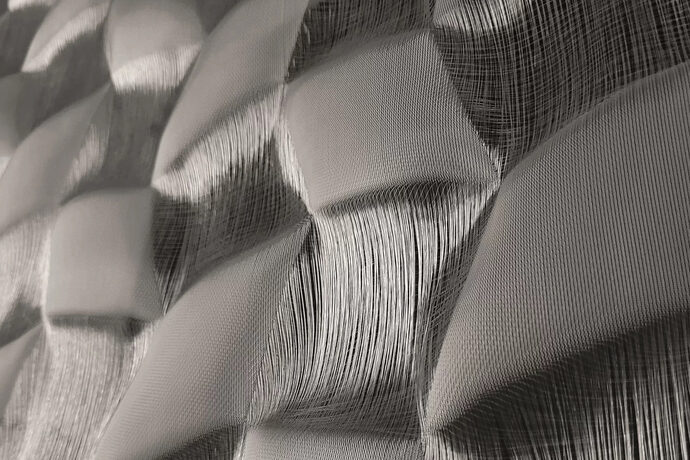
Tip: This year's Heimtextil University Contest gives young creatives the opportunity of a platform in Hall 3.0 in the New & Next area: finalists Rebecca Milautzcki, Tasja Videmšek and Svenja Bremen will be presenting their work. The themes of the textile concepts range from unconventional pattern dimensions and functional modular elements to fabrics as a means of communication. While Rebecca Milautzcki combines translucency, materiality and a three-dimensionality of weave structures, Tasja Videmšek has developed a modular tufted carpet that can be freely arranged into different compositions depending on the needs of the room. In her project, Svenja Bremen explores the potential of textiles as a means of communication, a carrier of meaning and a medium of memory.