Aug 22, 2013
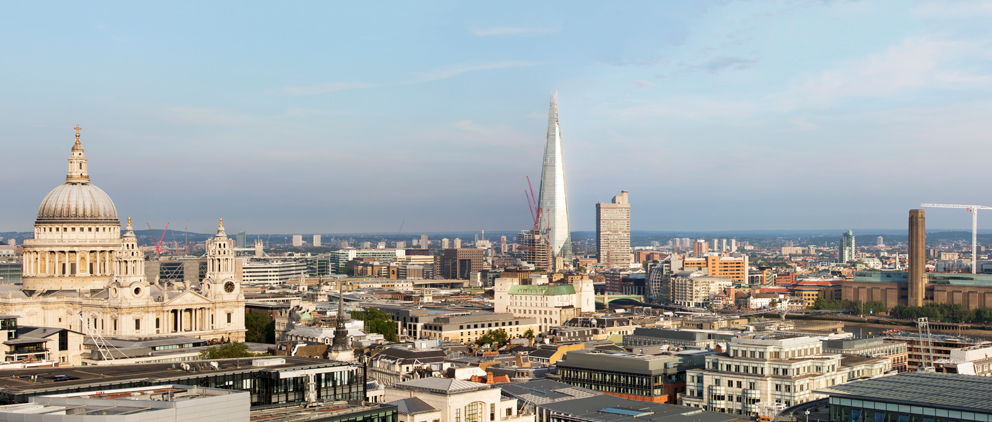
Bart Akkerhuis, project manager at Renzo Piano Building Workshop (RPBW), played a key role in the development of the outer skin for “The Shard”. So how do innovative processes between developers, architects and industry arise and how does this feed back into the design proposal? Julius Streifeneder talked with Bart Akkerhuis about how new types of facades get invented.
Julius Streifeneder: Before we start discussing the present, let’s take a look back: Can you describe the development that “Renzo Piano Building Workshop” (RPBW) has undergone over the years with regard to glass façades?
Akkerhuis: I think every façade we’re doing is somehow a development that is based on something we have built in the past. Aspects like transparency and sustainability were already important to us thirty, forty years ago. Our office has been involved in the development of double-skin façades with an emphasis of these topics since the beginning. Innovation in architecture is most of the time an evolutionary process. Some of the details we developed for example in Berlin – the office building at Potsdamer Platz – are still available on the building market. The Shard is an evolution from the Berlin project, where the cavity is made smaller to gain more usable space. I think that we developed the system of double-skin façades almost to its end. Now we are in the process of developing other systems with the industry, like the closed cavity façade, which we developed for our “Yongsan” project in Seoul. This is the next evolutionary step we are working on.
Can you describe the ground-breaking technological impulses along the way of the development of glass façades?
Akkerhuis: I think the permanent optimization of the façade systems is the driving objective – to design a façade that is very thin, very slim, and very transparent. There are other aspects like for example the maintenance of the cavity space. Now we’re getting façades where you don’t have to maintain the cavity at all. This is the next step. Then we go further to the closed-cavity cell, which is a little bit revolutionary again. I think one of the ground breaking technologies in the building industry was the introduction of glass coatings. Furthermore we see technological breakthroughs with what the industry can do with the sizes of pane curved glass, etc.
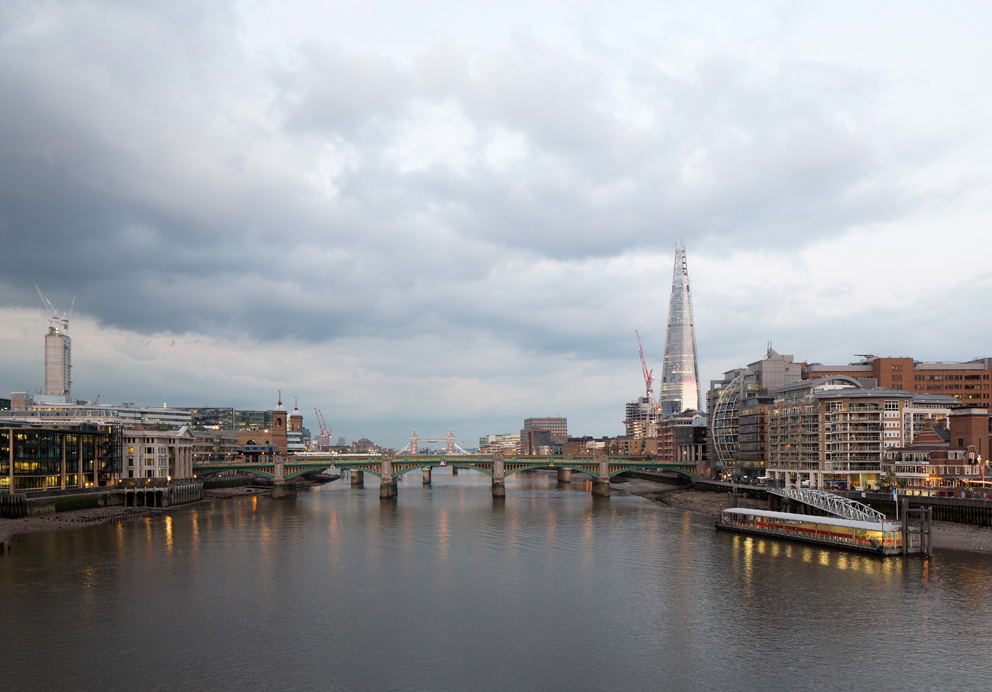
Do you think simulation software tools pushed the boundaries of façade design further?
Akkerhuis: As far as I can tell, the tools are helpful in design process, but it’s still difficult to predict the final performance of facade. That’s why we develop facades by collecting data from existing façades and from experience. That’s how it works for us, mostly. We at RPBW gain a lot of knowledge from our “old” façades by observing them and optimizing the elements. We already used basic and rudimentary software thirty years ago in the process of designing the “Menil Collection” in Houston, for studying sun path diagrams and solar shading.
So you are saying that ultimately the motor for innovation is the experience you draw from having built buildings?
Akkerhuis: Yes, quite often it’s not new technology that creates the innovation. I want to give an example. On the “Hermès” building in Japan we closely worked together with craftsmen to figure out the right material properties of glass blocks. There was so much knowledge, so much experience of the material and so much craftsmanship available that they were able to develop the glass blocks we needed for the facade with them because they knew how to push the boundaries of the material.
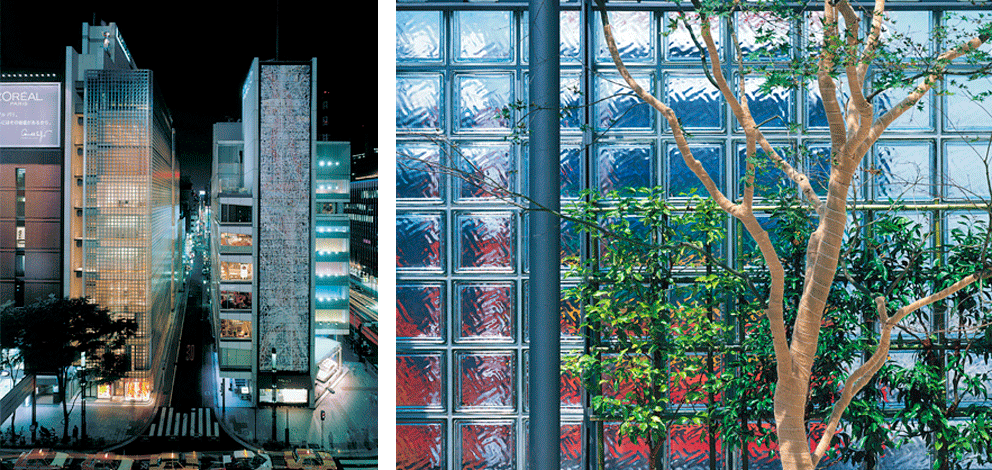
Akkerhuis: The challenge was of course that we designed a glass building. The “Shard of glass” was set up from the beginning. Basically the building has a certain shape and made of glass and nothing else. If you don’t get the shape right, it’s not good, but if you don’t get the glass right either, it’s very wrong. Of course the sustainability-aspect has been a big technological challenge. I think, we managed this quite well in the sense that the façade is very well-performing when it’s overcast. We need less artificial light because we have a lot of natural daylight. When it’s sunny, we put the blinds down and we have a very good solar control. It works very well in both extremes of weather. For a building of this size this is quite a challenge and we achieved it. But the “real” challenge was the architectural one: “how do we get shards of glass to look like shards of glass?” We had to get it right. That’s what we were concerned about. The process took three years to get the glass right.
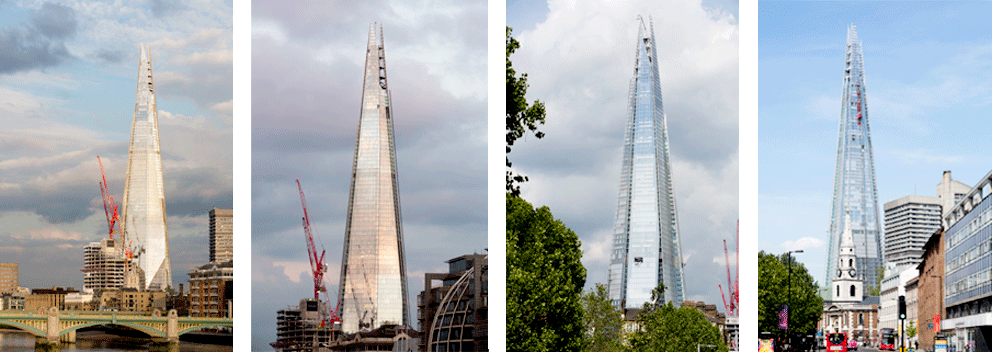
Akkerhuis: We in our office like transparency. Our buildings aspire to be as transparent as possible. So when we design a “shard of glass”, our first reaction is: “we need to have extra clear glass, as transparent as possible.” But when we had the first renderings done, the building looked dark and black. We felt that our building should look more shiny. We wanted to see the sky in it. We wanted to see a crystal building. And that’s when we realized we needed some kind of reflective coating. Not for solar control, but for architectural aesthetics, to get the reflectiveness we wanted. At the beginning of the design phase, it was really something we never expected. Historically, our office doesn’t use solar coating if it isn’t necessary. We would prefer to find alternative solutions. And here, we were putting a solar coating as an architectural ornament almost. It worked very well in the end.
The search for the solar coating was a real challenge. We needed something that is reflective, but still transparent, because it shouldn’t be a mirror building. It should be open and welcoming, not arrogant. Also we wanted the reflection to be as natural as possible. Take a look at the Shard now: You can see the same color of the sky reflected in the glass, without any distortion and you realize that the building adapts to the atmospheric lights and the sky. So for that we spent two or three years searching for the right solar coating and working with the façade manufacturer to ensure the glass is totally flat. First, we looked around to other buildings and ordered samples of products available on the market. Later on we talked to the industry and asked them what makes the coating reflective? What sort of metals do you use to get a certain reflectivity?
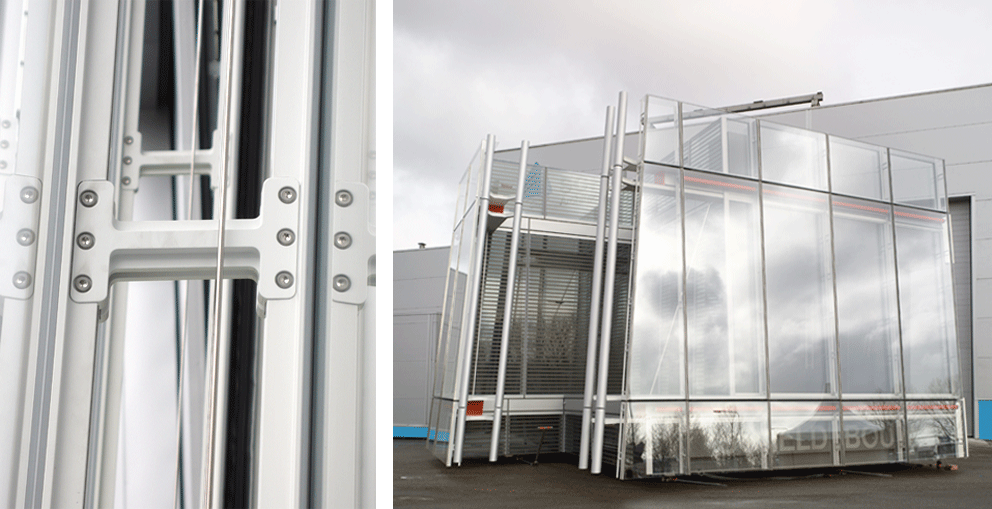
Akkerhuis: I don’t think we necessarily create something because we just are able to do it. I think we develop it because we think it makes sense. For the last forty years, sustainability has always been high on our agenda in our office. So when we designed “the Shard”, an uncompromising glass tower, we knew, we can be criticized very easily if we don’t make it technically convincing. But it won’t work the other way around: you don’t want to aim for the most technologically advanced façade in the industry and then think of the architecture. It is not a very good argument just to do something because it’s technically possible but without any functional reason for it.
It makes me think a little bit of Piano’s IBM Pavilion back in the eighties - the barrel vaulted pavilion with a timber frame and the polycarbonate tiles in it. That was a very experimental building from what I recall, in every way.
Indeed, it is an experimental building. And Renzo experimented with the technique already in the sixties before eventually executing it in the eighties. The great thing about it was, that the polycarbonate was part of the stiffness of the structure. And here again, it is born out of a desire to make a very transparent pavilion and the idea that you would be in contact with your surroundings. Because it was a pavilion that should be able travel it was necessary that it was light, and demountable. So the technical innovation comes from those essential needs, not just because we can do stuff.
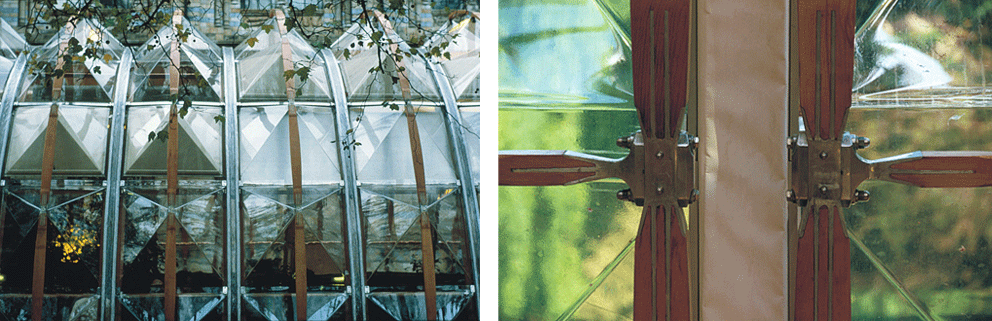
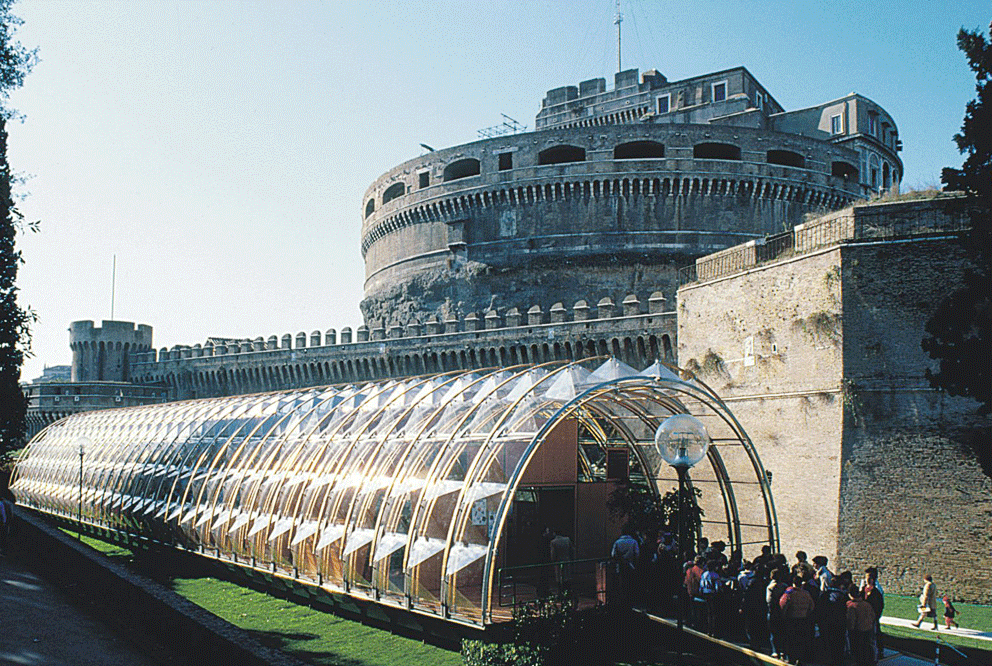
Akkerhuis: In our research for the Shard-façade, we saw a façade in Berlin that had some of the ideas we were talking about. We went to the industry with our wish list: “That’s the coating we want, but a bit different – a bit more neutral, a little less reflective and on extra-white glass. Can you do it?” There were a few that said ‘Yes’ and they gave us samples from their existing catalogue that came close, but there was only one who was open to work with us to give us exactly what we wanted.
We developed the coating with them. They had the willingness to invest their energy in it ¬– because they thought: “Well if this building ever goes ahead, it is a great opportunity.” And now I think at the moment it’s one of the most requested coatings for architectural glass in Europe.
Which role in this innovation processes does the client play?
Akkerhuis: A good client is a client that we have a lot of discussion with. Renzo always says: “Great clients are clients who will play ping-pong with us.” With a good client we have a lot of interaction and they give a lot of feedback. On the Shard-Project, we had a very supportive client giving us a lot of freedom. We were also lucky with the planning authorities. For the planning application we showed the reflectiveness, the transparency and the whiteness of the glass and the client and Southwark council were very enthusiastic.
Although at that point we didn’t quite know how to achieve it yet, we knew this is something that we had to do! We couldn’t just make an assembly of the building with green glass and darker coating or something. There was no way back. The client and the public expected this from us. So in that sense, we had a very good foundation to push the boundaries and create technological innovations in an architectural project like this.
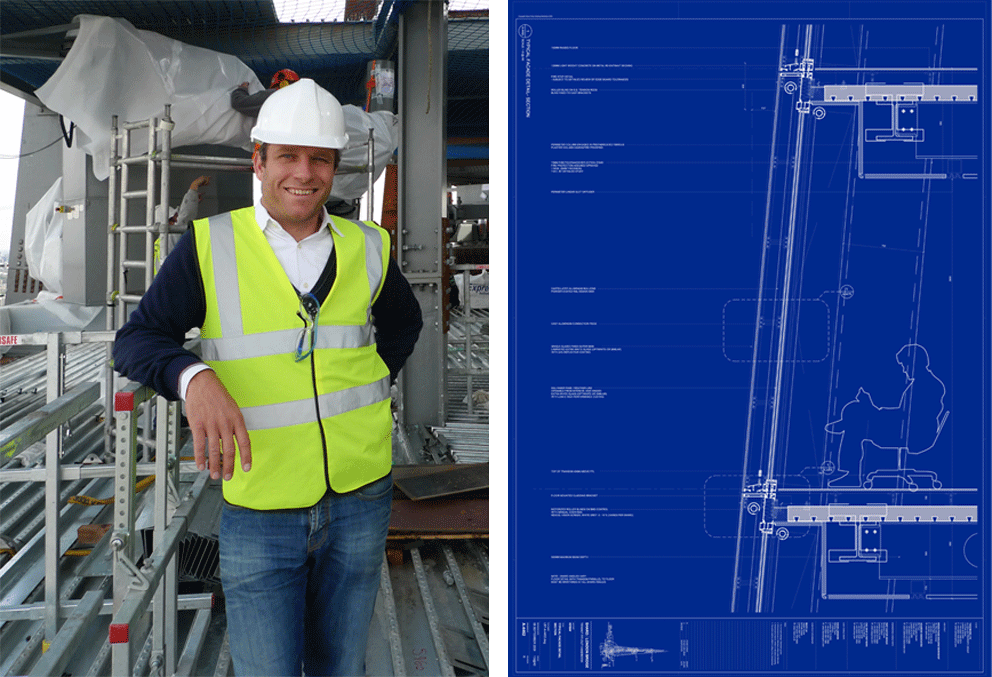
› All façades are essentially media façades
› The adaptable house
› NO NO NO NO NO The book to go with the Seagram Building
› Good illumination
› The Selfi-Façade